DEALKALIZATION UNIT
Innovative water treatment solutions are provided by Larco India Pvt Ltd, a reputable dealkalization unit in Pune. Using cutting-edge technologies like ion exchange resin, cation exchange resin, anion exchange resin, and ion exchange membranes to produce excellent outcomes is our area of expertise.
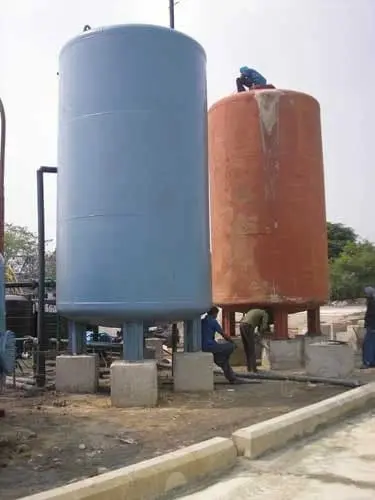
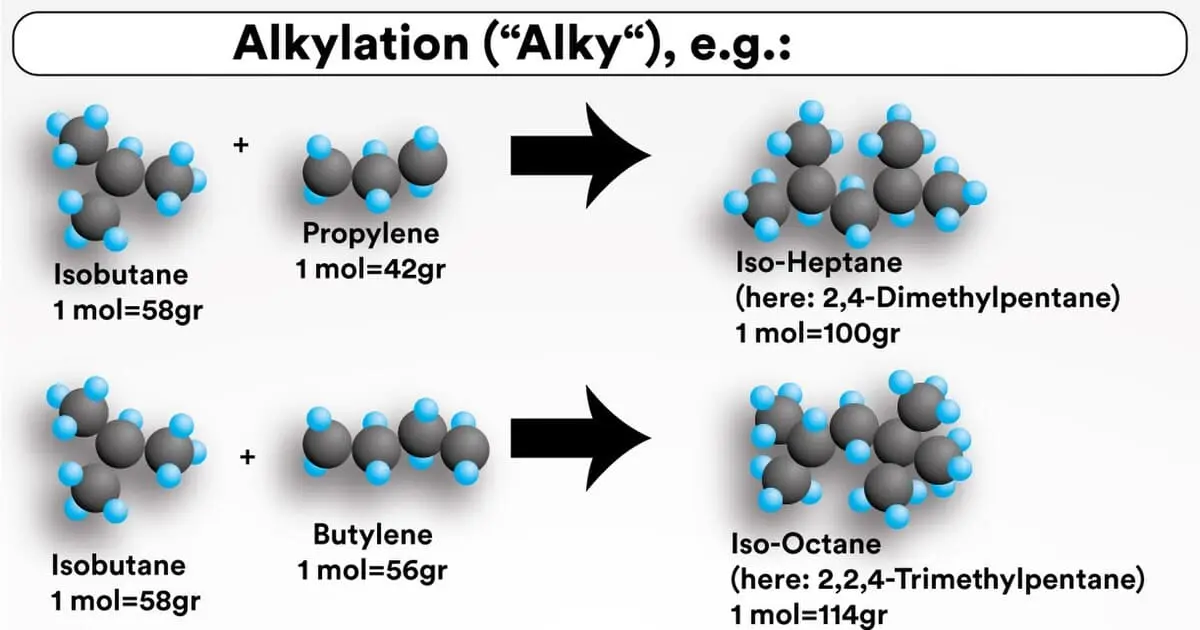
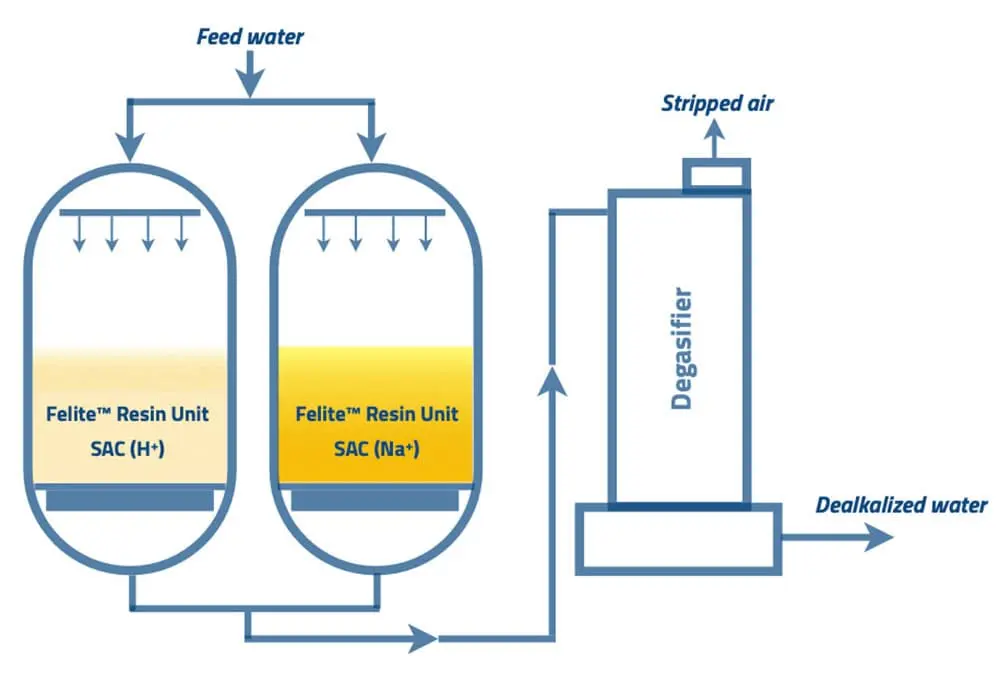
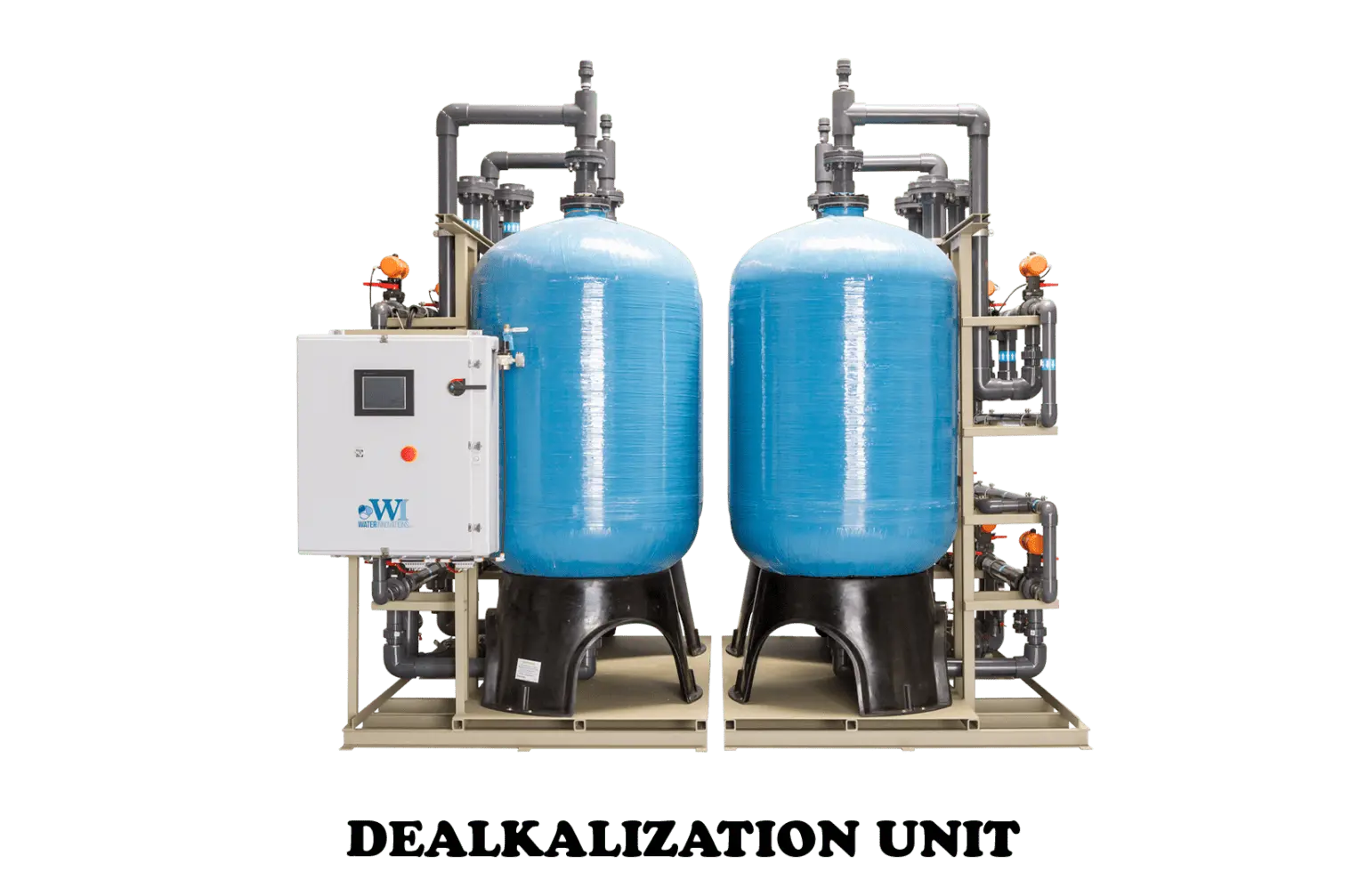
What is a dealkalization unit?
A dealkalization unit, also known as an ion exchange unit or a demineralization unit, is a component of a water treatment system used to reduce the alkalinity and mineral content of water. It uses an ion exchange process. In industrial and commercial settings, this type of technology is typically used to produce water that is devoid of alkaline compounds and minerals like calcium and magnesium.
How does a dealkalization unit work?
In order to remove alkaline chemicals from water, a dealkalization unit, often referred to as an anion exchange unit, uses ion exchange resin.
Ion Exchange Resin: The ion exchange resin acts as the brain of a dealkalization unit. This resin is made up of small beads with a chemical charge that draw and swap certain ions in water. In this instance, the resin is made to exchange chloride ions for alkalinity-contributing bicarbonate ions.
Dealkalization Process: Bicarbonate ions in the water are drawn to and replaced by chloride ions on the resin beads as it passes through the ion exchange resin bed. The alkalinity of the water is efficiently decreased by this exchange.
Regeneration: The ion exchange resin fills up with bicarbonate ions and other minerals over time. The resin needs to be regenerated in order to carry on with the dealkalization procedure. In order to accomplish this, the resin bed is often flushed with a solution containing concentrated chloride ions. The surplus minerals are washed away as the chloride ions displace the bicarbonate ions in the resin.
Usage and Maintenance: The dealkalization device can continue treating water after the resin has been regenerated. The capacity of the system and the mineral concentration of the water both affect how frequently the system regenerates. To make sure the unit runs efficiently and consistently, proper maintenance and monitoring are essential.
Applications of Deealkalization unit
Boiler Feed Water:
Reducing mineral buildup is crucial in steam-generating systems to avoid scale formation and maintain boiler efficiency.
Cooling Towers:
Dealkalized water can assist in preventing the growth of scale and lowering the risk of corrosion in cooling systems.
Detergent Manufacturing:
Low-mineral water is preferable to prevent interference with the cleaning process when making high-quality detergents and cleaning solutions.
Electronics Manufacturing:
Extremely pure water is needed in some electronic manufacturing processes to avoid contamination and guarantee product quality.
Dealkalization devices can be made to interact with other water treatment systems, including softeners and filter units, to produce desired water qualities. They are customized to meet specific water quality requirements.
Advantages of dealkalization units
To remove alkalinity from water, a water treatment system called a dealkalization unit—also known as a dealkalizer or anion exchange unit—is used. In industrial processes, boiler systems, and other applications, high levels of alkalinity can lead to a number of issues. Bicarbonates, carbonates, and hydroxides are common forms of alkalinity in water. The following advantages come from using a dealkalization unit in Pune.
Boiler and Equipment Protection: Dealkalization helps stop scale from forming in boilers and other heat exchangers. Scale buildup makes heat transfer less efficient, resulting in higher energy costs and potentially equipment damage.
Reduced Corrosion: The protective oxide coating on metal surfaces may become unstable at high alkalinity levels, which may promote corrosion in pipelines and other equipment. Dealkalization lengthens the equipment’s lifespan and lowers maintenance costs, both of which contribute to lowering this risk.
Improved Boiler Efficiency: By reducing scale and corrosion, dekalinization raises the overall efficiency of boiler systems. Heat transfer surfaces that are cleaner and perform better lead to lower fuel use and operating costs.
Enhanced Steam Purity: Reducing alkalinity helps to maintain the purity of steam produced by boilers. When contaminants such as dissolved solids and pollutants are reduced in alkaline water, high-quality steam can be produced for a range of processes.
Prevention of Carryover: Carryover, or the entrainment of water droplets with steam, can be problematic for processes farther down the line. Dealkalization produces steam with lower impurity levels, which reduces carryover.
Consistent Product Quality: In industries where water quality is crucial for the manufacture of goods, dealkalization ensures consistent water quality that meets predetermined parameters. The manufacturing of electronics, pharmaceuticals, foods, and beverages all depend on this.
Environmental Considerations: Reduced scale growth and corrosion reduce the need for potentially dangerous chemical additives. Dealkalization aids in making water treatment more sustainable and environmentally responsible.
Cost Savings: Despite the initial expense of a dealkalization unit, the long-term benefits in terms of reduced maintenance, extended equipment life, and energy savings typically outweigh the initial expenditures.
Regulatory Compliance: In many industries, there exist guidelines and specifications for emissions and water quality. Dealkalization can help companies follow these regulations by maintaining appropriate water quality.
Customization: Dealkalization unit in Pune can be constructed and altered to meet specific water quality and capacity requirements, making them flexible for a variety of industrial processes and applications.
It is important to keep in mind that factors such as the water’s composition, flow rates, and the specific requirements of the application can affect how effective a dealkalization unit is Prior to implementing a dealkalization system, a thorough analysis of the water chemistry and process requirements is necessary to determine the optimal alternative.